Investment casting is usually a method of obtaining castings by coating several layers of refractory material on the surface of wax molds, allowing them to harden and dry. The wax molds are melted off to form a shell, which is then baked and poured. Due to the high dimensional accuracy and surface finish of the obtained castings, it is also known as “investment casting precision casting”. This article mainly analyzes the manufacturing methods, advantages, and development history of investment casting comprehensively.
The first process of investment casting production is to manufacture investment molds, which are used to form models of refractory shell cavities. Therefore, in order to obtain castings with high dimensional accuracy and surface smoothness, investment molds themselves should have high dimensional accuracy and surface smoothness. In addition, the performance of the investment mold itself should also be as simple and feasible as possible for subsequent processes such as shell making. In order to obtain the high-quality investment molds required above, in addition to good molding, it is also necessary to choose suitable mold making materials and reasonable mold making processes.
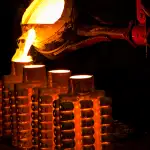
The advantages of investment casting are mainly reflected in two aspects:
- Due to the high dimensional accuracy and surface smoothness of investment castings, mechanical processing work can be reduced. Only a small amount of machining allowance can be left in the parts with higher requirements, and even some castings can be used without mechanical processing, leaving only grinding and polishing allowance. It can be seen from this that using investment casting method can greatly save machine equipment and processing time, and greatly save metal raw materials.
- Investment casting can cast complex castings of various alloys, especially high-temperature alloy castings. Production using investment casting technology can not only achieve mass production, ensuring the consistency of castings, but also avoid stress concentration caused by residual tool lines after mechanical processing.
The development history of investment casting:
Investment casting has been developing at a relatively fast pace for half a century since it became suitable for industrial production in the 1940s. In 1996, the world’s investment casting industry accounted for 50% in North America, 25% in Europe, 20% in Asia, and the remaining 5%. In North America, the United States accounted for 95%, while in Europe, the United Kingdom accounted for 42%, France accounted for 26%, Germany accounted for 19%, Italy accounted for 7%, and the remaining 6%. Nowadays, investment casting is widely used in almost all industrial sectors, especially in electronics, petroleum, chemical, energy, transportation, light industry, textiles, pharmaceuticals, medical equipment, pumps, and valves, except for aviation and weapons. Due to the unique advantages of investment casting in the industrial production field, the current development speed of investment casting is extremely fast.
Disclaimer: Some of the content in this article is reproduced online, and the copyright belongs to the original author. If there are any copyright issues related to the work, please contact us. We will confirm the copyright based on the copyright proof materials you provide and delete or take relevant measures within one week of receiving the proof!
Link to this article:Comprehensive Analysis of Investment Casting
Reprint Statement: If there are no special instructions, all articles on this site are original. Please indicate the source for reprinting.:ODM Wiki,thanks!^^